As snow and ice management face increasing demands for efficiency, liability reduction, and environmental responsibility, advanced spreader technologies are stepping up to revolutionize the industry. From precise material control to real-time data tracking, these innovations are transforming how contractors approach salt application, making operations smarter and more sustainable.
October 22, 2024 | Craig Sandmann, Snow Plow News Guest Editor
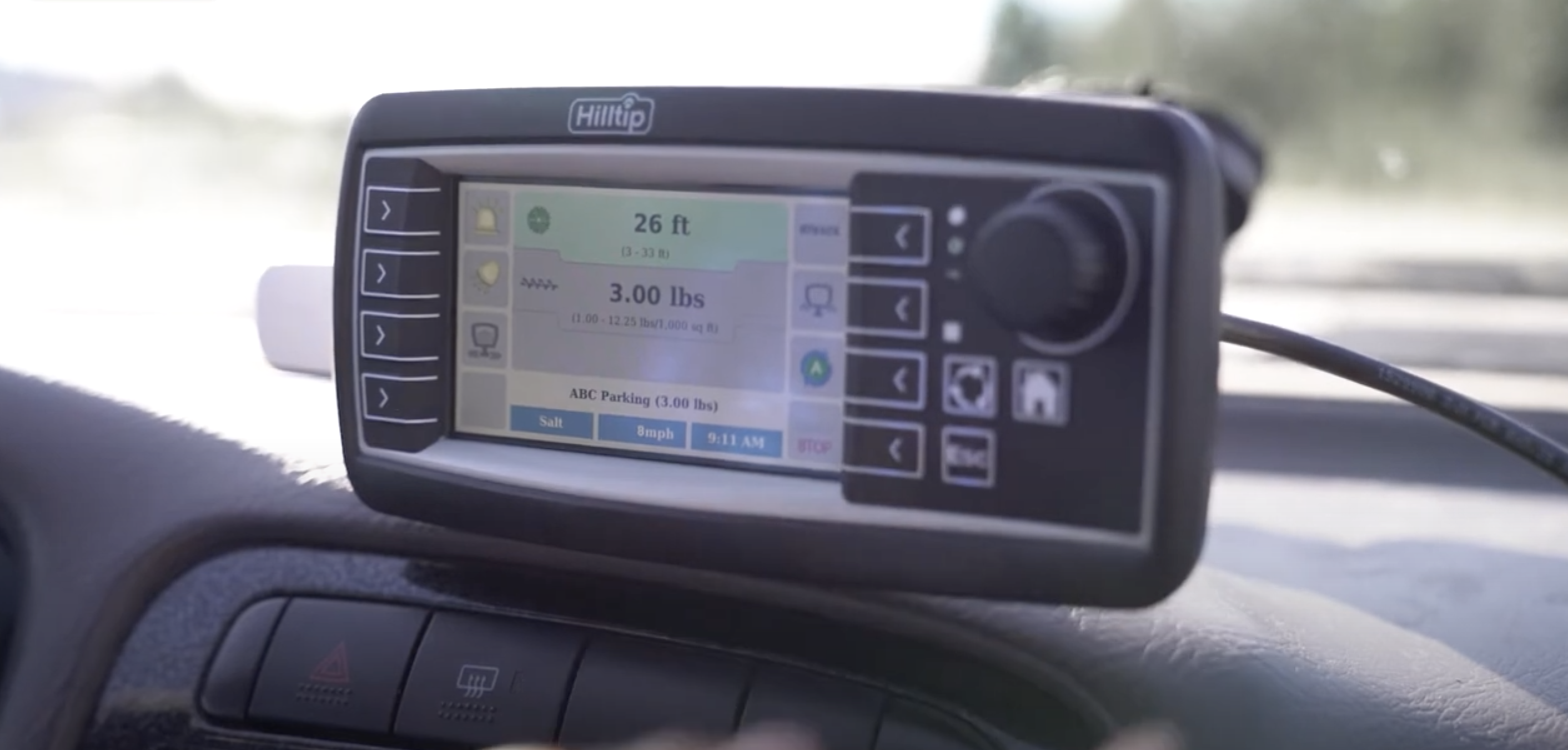
Though many wouldn’t immediately think so, the snow and ice management sector is on the brink of a technological transformation. Contractors today are under rising pressure to enhance efficiency, cut down on labor, minimize liability, and reduce environmental impact when applying salt.
These challenges can be tackled through cutting-edge electronic controls. While systems with features like two-way GPRS tracking, advanced cab-based controllers, detailed data logging, and liquid integration may require a larger initial investment, their long-term advantages are undeniable. Equipment distributors that offer these advanced snow and ice solutions are likely to see a surge in demand.
Boosting Efficiency
Setting aside initial capital investments, the two biggest expenses in snow and ice control typically come down to deicing materials and time spent on the job. Modern technologies can significantly cut both.
Take, for example, spreaders that incorporate advanced GPS tech. Hilltip’s HTrack™ system, for instance, uses Google maps. A contractor can enter the service location, set up geo-markers on a satellite view, and define the service area. Once done, the software calculates how much material is needed and the time required to complete the job. If the application rate is predetermined, the system can automatically adjust, leaving only the driving to the operator.
This technology simplifies the task, but its real strength is seen over time. Contractors handle multiple sites, and a common time-waster is running out of materials mid-job and needing to return for resupply. A system that calculates material requirements in advance not only saves time and resources on each job but also helps streamline the service route to avoid unnecessary trips. With this efficiency, a contractor might go from handling two or three sites before resupplying to covering four or five. These improvements save materials and labor while also offering intangible benefits such as less fuel consumption, reduced tire wear, fewer brake repairs, and lower overtime costs.
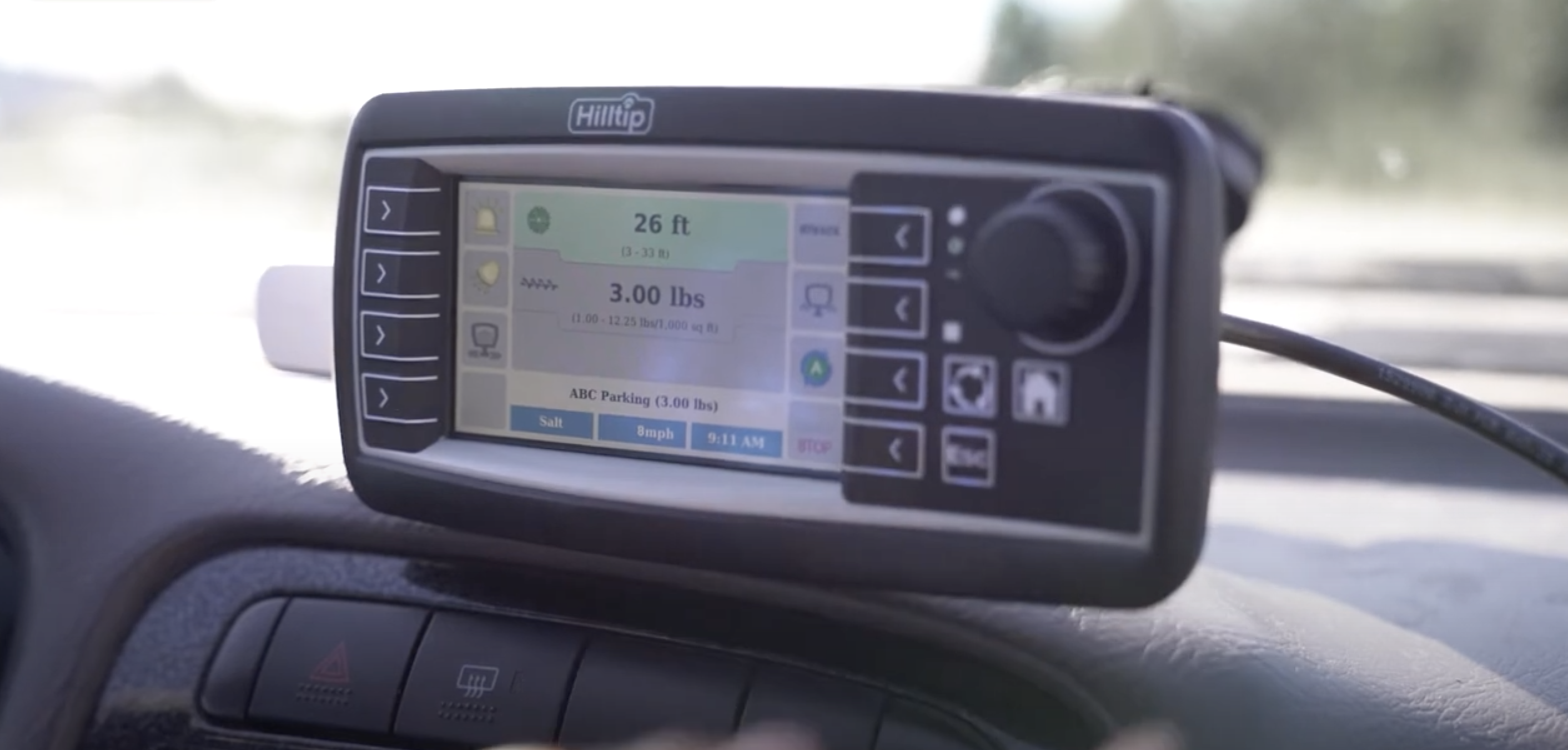
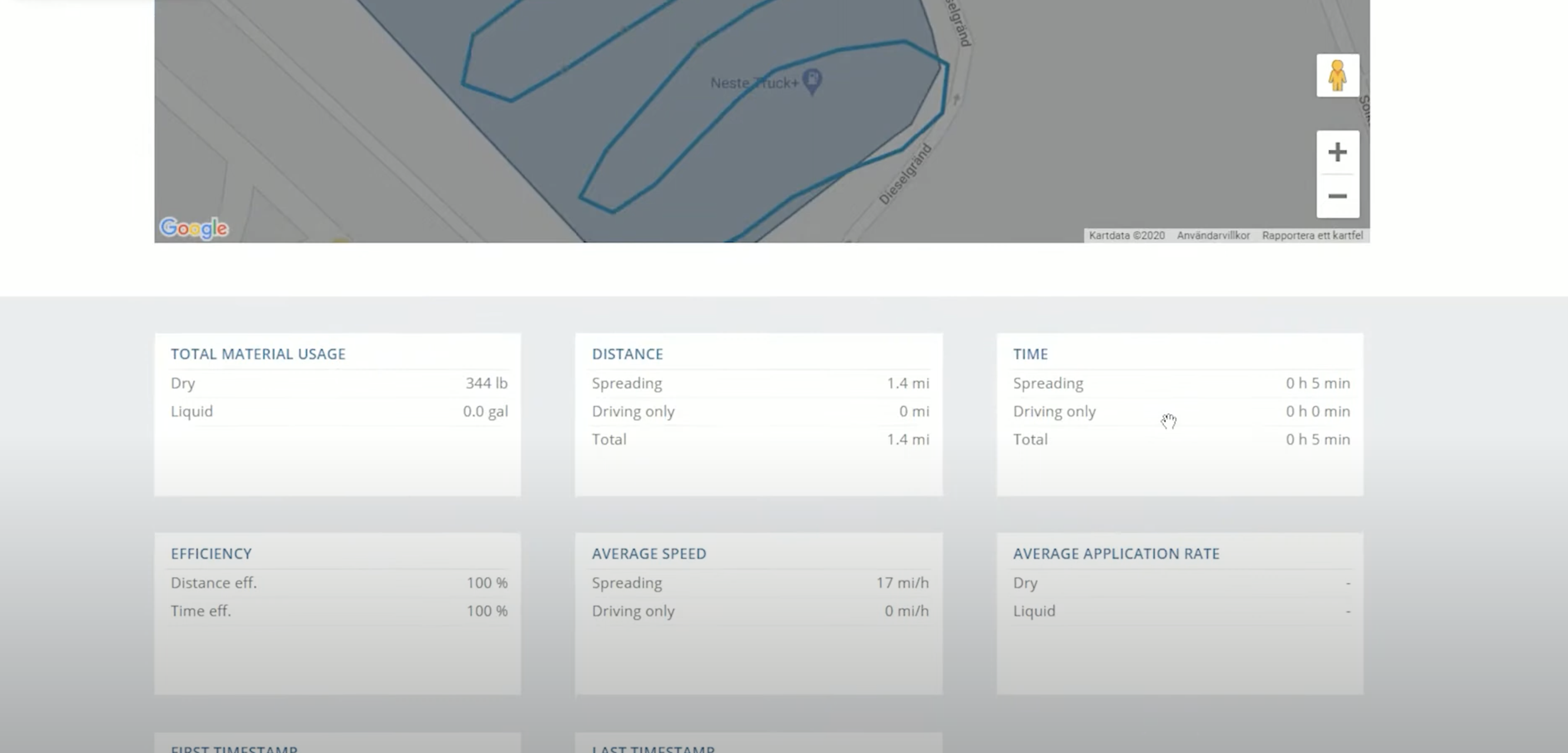
Addressing Labor Challenges Labor shortages are a growing problem, but advancements in snow and ice management tech reduce both the amount of labor required and the experience needed.
When machines work more efficiently and jobs are planned based on accurate data, fewer labor hours are required. Once a contractor knows the material amount needed for a site, these systems handle the rest. They eliminate guesswork in material distribution and site coverage.
Additionally, these systems make the work accessible to a broader pool of candidates and more enjoyable. Since the tech handles more of the workload, contractors are under less pressure to find experienced operators. Even common tasks like activating the spreader’s vibrator to release material can now be automated. In short, all the operator needs to focus on is driving.
Another significant labor concern is not knowing what happens once the team leaves the shop. Is the operator taking the best route? Are they covering the entire site properly? Did they leave the spreader running between sites, wasting material? Are they taking detours for personal stops? Previously, there was no way to know without visiting the site. But now, advanced spreaders constantly send data to the cloud, where it can be monitored in real-time or saved for future reference. Two-way GPRS control even allows contractors to remotely manage the spreader while it’s on-site, a huge advantage with less experienced operators. This data is also valuable for employee performance reviews.
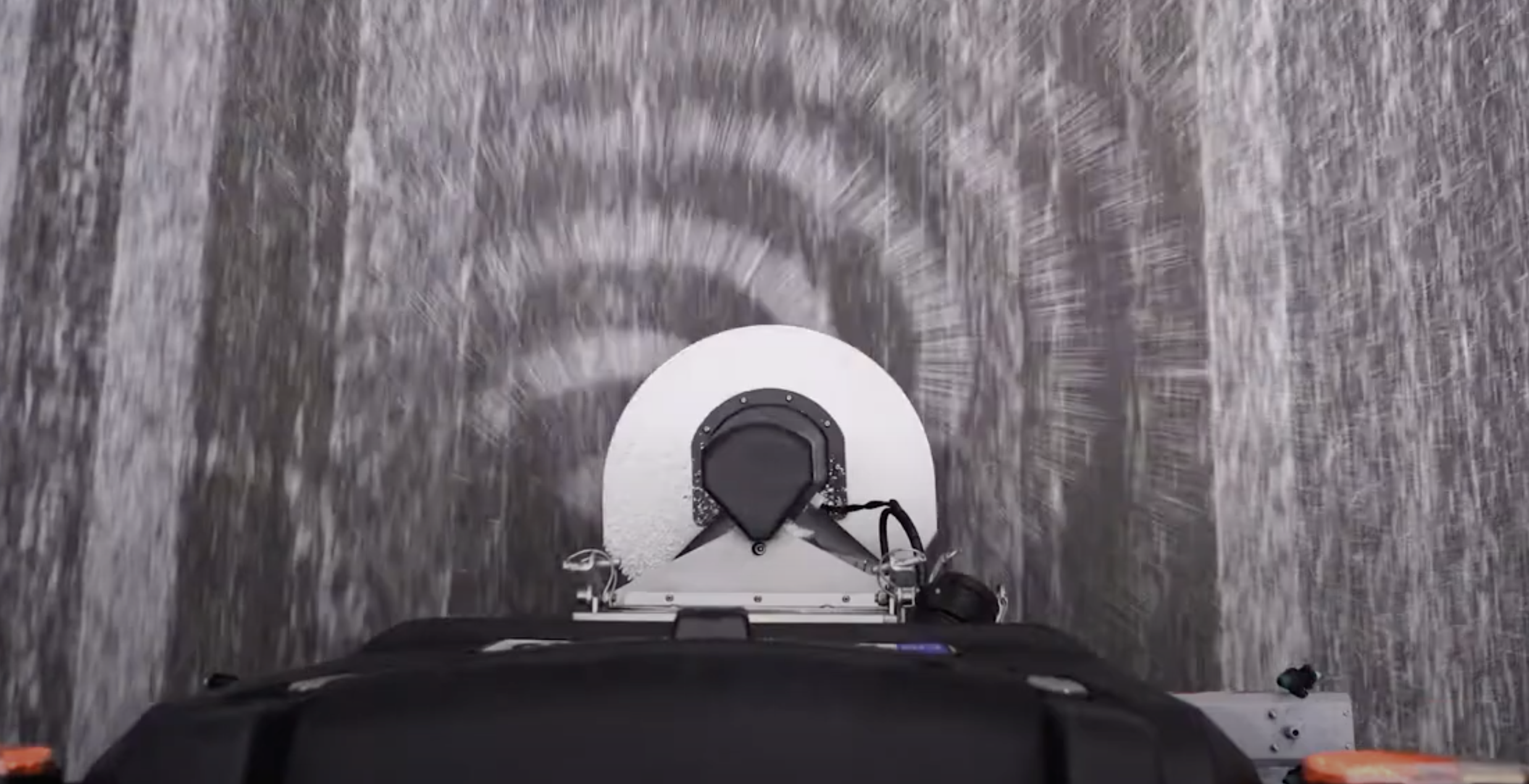
Mitigating Liability
One of the most significant benefits of advanced data collection is reducing liability. When a slip-and-fall incident occurs, blame often follows. While having service data doesn’t guarantee immunity from blame, it greatly diminishes the contractor’s liability. These systems record when an operator arrives on-site, when the job is finished, where material was spread, how much was used, and more. Advanced GPS systems can even detail the exact amount of material spread where an incident occurred.
From the property owner’s perspective, this kind of documentation also lowers their liability. If a contractor offering this level of detail is competing against one who doesn’t, all other things being equal, who do you think will win the contract?
Reducing Environmental Impact
Aside from liability, environmental concerns are also becoming a major issue in snow and ice management. Whether contractors feel responsible or not, many clients are pushing for greener operations, and it won’t be long before legislation limits the use of chlorides in deicing.
Once again, advanced spreader tech is ahead of the curve. Being able to precisely control the amount of material applied, while also documenting it, ensures that environmentally-friendly practices are followed. Many of today’s spreaders also integrate liquid treatment.
Modern spreaders, often called “combi” spreaders, come equipped with liquid tanks, allowing operators to pre-wet granular materials with a brine solution as they spread or directly treat the surface with liquids.
This reduces the amount of salt needed to achieve the same results by up to 30%, cutting down on chlorides entering the environment. Pre-wetting also helps keep materials in place, minimizing runoff into grass, ditches, and waterways, which ultimately protects the watershed.
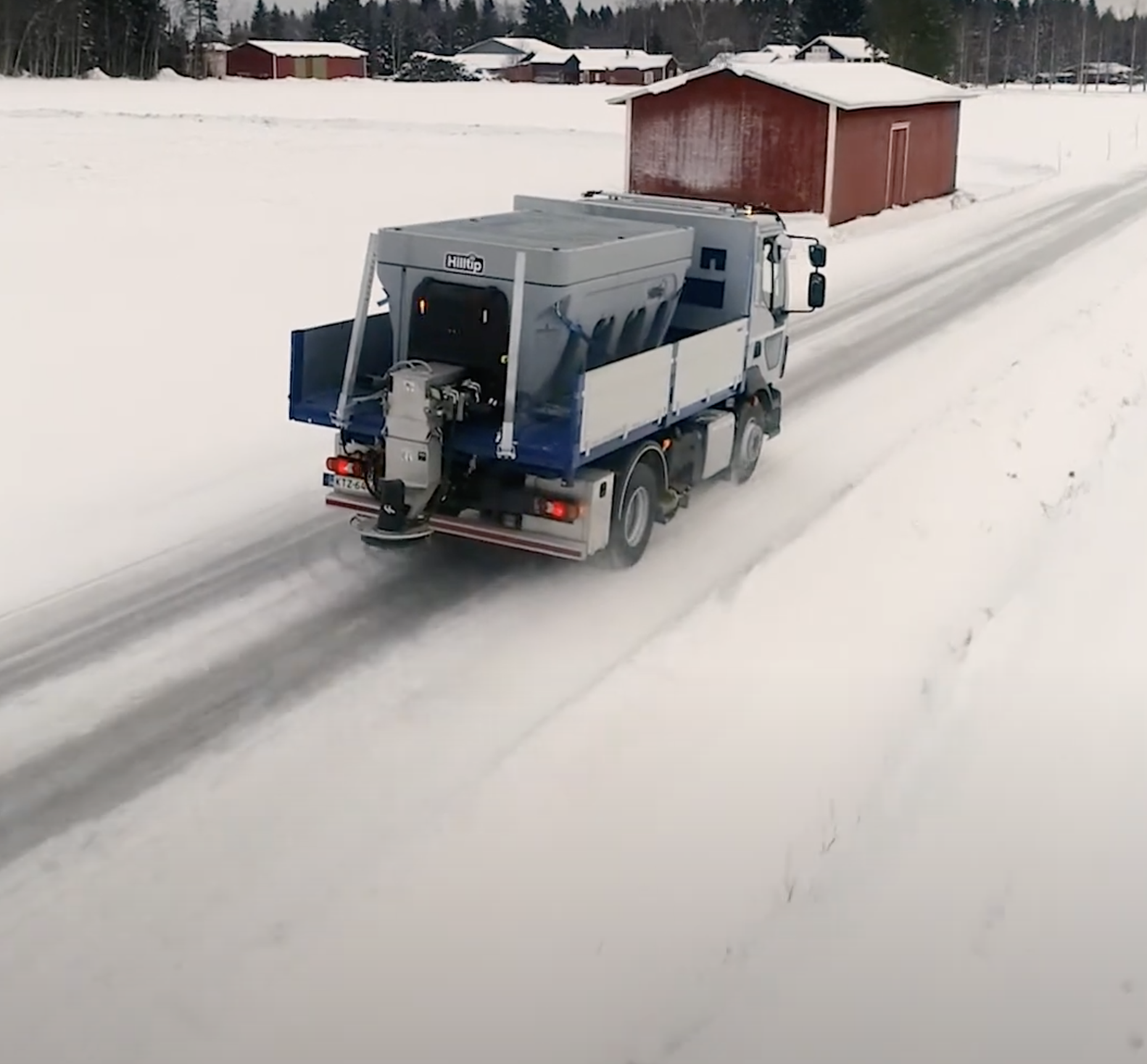
Economic Gains
These methods also offer financial benefits. Reducing salt usage by 30% equates to 30% in cost savings, directly boosting the bottom line. When bidding on new jobs, this gives a competitive edge. If Contractor A uses standard equipment and Contractor B integrates liquids, both may bid the same amount for the job, but Contractor B will see more profit. Plus, environmentally-conscious clients will likely choose the greener option.
Leading the Way
Snow and ice control has long been subjective. While the goal—clear pavement—is clear, achieving it has involved a mix of experience, gut feeling, and trial and error. But with advanced tech, subjective decisions are being replaced by data-driven precision, making it easier to consistently achieve the desired results. The more data gathered over time, the more efficient, effective, and profitable an operation becomes. Though it’s only a matter of time before all spreaders are this sophisticated, early adoption gives equipment distributors a short-term advantage that will be tough to beat long-term.
To learn more about Hilltip machines and technology, visit www.hilltipna.com
About the Author
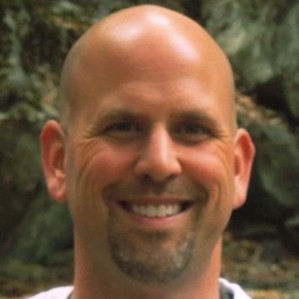
Craig Sandmann is the Managing Director of Hilltip Corp in North America. Based in Fort Wayne, IN Hilltip is a leading manufacturer of snow and ice control equipment that is known in the industry for advanced technologies and extreme durability.
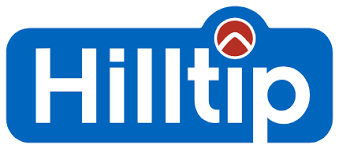
Want more information on this?